Principle of laser cutting
The laser beam is focused into a small point of light to achieve a high power density at the focal point. At this time, the heat input of the beam (converted by light energy) far exceeds the reflected, conducted and diffused part of the material,which is quickly heated to the vaporization temperature to form a hole.As the beam moves linearly relatively to the material,the holes continuously form a slit of a very narrow width.
Characteristics of laser cutting
1. The characteristics of laser cutting machine: Narrow slit, small deformation, high precision, fast speed and high efficiency.
2. Laser energy is converted into amazing heat energy which can keep in a very small area, so laser cutting can provide narrow straight edge slit, the smallest heat-affected zone near the cutting edge, and tiny local deformation.
3. The laser beam does not exert any force on the workpiece, and it is a non-contact cutting, which means that there is no mechanical deformation to the workpiece, no deformation of cutting tool and no replacement demand of cutting tool. It doesn’t need to consider the hardness of the material while cutting, the ability of laser cutting is not affected by the hardness of the material.
4. The laser beam is highly controllable and has high adaptability and flexibility, making it easy to realize the automatic production of cutting.
Main configurations
No. |
Name |
Brand |
Quantity |
Producing place |
1 |
Laser source |
MAX |
1 |
China |
2 |
Cutting head |
WSX |
1 |
China |
3 |
Precision rack |
JT |
3 |
Taiwan,China |
4 |
Reducer |
TECHMECH |
3 |
Germany |
5 |
Servo motor |
DELTA |
4 |
Taiwan, China |
6 |
Precision guide/lead screw |
SHAC |
4 |
Taiwan, China |
7 |
Numerical control system |
Friendess Electronics |
1 |
China |
8 |
Electrical control |
Omron/Schneider/Airtac |
1 |
Japan/France/Taiwan, China |
9 |
Chiller |
HanLi HL-3000 |
1 |
China |
10 |
Machine tool |
DP laser |
1 |
China |
Technical parameters
No. |
Performance parameters |
1 |
Laser power |
3000W |
2 |
Processing range (L*W) |
3000mm×1500mm |
3 |
X-axis travel |
1520mm |
4 |
Y-axis travel |
3020mm |
5 |
Z-axis travel |
260mm |
6 |
X/Y single axis positioning accuracy |
0.02mm/m |
7 |
X/Y axis repeated positioning accuracy |
+0.02mm |
8 |
Maximum speed |
110m/min |
9 |
Maximum acceleration |
1.5G |
10 |
Numerical control system type |
Bus control |
11 |
Maximum load capacity of workbench |
900kg |
12 |
Phase number |
3 |
13 |
Rated supply voltage |
380V |
14 |
Frequency |
50Hz |
15 |
Protection level of main power supply |
IP54 |
MFSC-3000(50μm) Cutting Parameter |
Material |
Thickness(mm)
|
Gas |
Speed(m/min)
|
Power(W)
|
Frequency(Hz)
|
Duty cycle(%)
|
Pressure(bar)
|
Cutting Height(mm)
|
Focus |
Nozzle |
Carbon Steel (Q235B)
|
1 |
N2/Air |
47~50 |
3000 |
5000 |
100 |
12~16 |
0.5 |
0 |
Single:1.0
|
2 |
N2/Air |
21~23 |
3000 |
5000 |
100 |
12~16 |
0.5 |
0~-0.5 |
Single:1.5
|
3 |
N2/Air |
6~12 |
3000 |
5000 |
100 |
12~16 |
0.5 |
-1~-1.5 |
Single:3.0
|
O2 |
3.9~4.1 |
3000 |
5000 |
100 |
0.6~0.9 |
0.8 |
4.5~5.5 |
Double:1.2
|
4 |
O2 |
3.4~3.6 |
3000 |
5000 |
100 |
0.6~0.9 |
0.8 |
4.5~5.5 |
Double:1.2
|
6 |
O2 |
2.7~2.8 |
3000 |
5000 |
100 |
0.6~0.9 |
0.8 |
4.5~5.5 |
Double:1.2
|
8 |
O2 |
2.1~2.3 |
3000 |
5000 |
100 |
0.6~0.9 |
0.8 |
4.5~5.5 |
Double:1.2
|
10 |
O2 |
1.4~1.6 |
3000 |
5000 |
100 |
0.6~0.9 |
0.8 |
4.5~5.5 |
Double:1.4
|
12 |
O2 |
1~1.1 |
2200~2400 |
5000 |
100 |
0.6~0.9 |
1.5 |
2~3 |
Double:3.0
|
14 |
O2 |
0.9~0.95 |
2200~2400 |
5000 |
100 |
0.6~0.9 |
1.5 |
2~3 |
Double:4.0
|
16 |
O2 |
0.8~0.85 |
2200~2400 |
5000 |
100 |
0.6~0.9 |
1.5 |
2.5~3.5 |
Double:4.0
|
18 |
O2 |
0.7~0.72 |
2200~2400 |
5000 |
100 |
0.6~0.9 |
1.5 |
2.5~3.5 |
Double:4.0
|
20 |
O2 |
0.6~0.65 |
2200~2400 |
5000 |
100 |
0.6~0.9 |
1.5 |
2.5~3.5 |
Double:4.0
|
22 |
O2 |
0.55 |
2200~2400 |
5000 |
100 |
0.6~0.9 |
1.5 |
2.5~3.5 |
Double:4.0
|
25 |
O2 |
0.5 |
2200~2500 |
5000 |
100 |
0.6~0.9 |
1.5 |
2.5~4 |
Double:5.0
|
Stainless Steel (SUS304)
|
1 |
N2/Air |
50~53 |
3000 |
5000 |
100 |
12~16 |
0.5 |
0 |
Single:1.5
|
2 |
N2/Air |
23~25 |
3000 |
5000 |
100 |
12~16 |
0.5 |
0~-0.5 |
Single:2.0
|
3 |
N2/Air |
10~12 |
3000 |
5000 |
100 |
12~16 |
0.5 |
-1~-1.5 |
Single:3.0
|
4 |
N2/Air |
6~8 |
3000 |
5000 |
100 |
12~16 |
0.5 |
-2~-2.5 |
Single:3.0
|
6 |
N2/Air |
2.9~3.1 |
3000 |
5000 |
100 |
12~16 |
0.5 |
-3.5~-4 |
Single:3.0
|
8 |
N2/Air |
1.2~1.3 |
3000 |
5000 |
100 |
16~18 |
0.5 |
-5~-6 |
Single:3.0
|
10 |
N2/Air |
0.75~0.8 |
3000 |
5000 |
100 |
16~18 |
0.5 |
-6.5~-7 |
Single:4.0
|
12 |
N2/Air |
0.5 |
3000 |
5000 |
100 |
16~18 |
0.5 |
-7.5~-8.5 |
Single:4.0
|
Aluminium |
1 |
N2/Air |
40~43 |
3000 |
5000 |
100 |
12~16 |
0.5 |
0 |
Single:1.0-1.5
|
2 |
N2/Air |
16~18 |
3000 |
5000 |
100 |
12~16 |
0.5 |
0~-0.5 |
Single:1.5-2.0
|
3 |
N2/Air |
8~10 |
3000 |
5000 |
100 |
12~16 |
0.5 |
0~-0.5 |
Single:2.0-3.0
|
4 |
N2/Air |
5~6 |
3000 |
5000 |
100 |
12~16 |
0.5 |
-1~-1.5 |
Single:3.0
|
6 |
N2/Air |
1.5~2 |
3000 |
5000 |
100 |
12~16 |
0.5 |
-2~-3 |
Single:3.5-4.0
|
8 |
N2/Air |
0.6~0.7 |
3000 |
5000 |
100 |
16~18 |
0.5 |
-3~-4 |
Single:4.0
|
Brass |
1 |
N2/Air |
37~40 |
3000 |
5000 |
100 |
12~16 |
0.5 |
0 |
Single:1.0-1.5
|
2 |
N2/Air |
14~16 |
3000 |
5000 |
100 |
12~16 |
0.5 |
0~-0.5 |
Single:1.5-2.0
|
3 |
N2/Air |
7~9 |
3000 |
5000 |
100 |
12~16 |
0.5 |
0~-0.5 |
Single:2.0-3.0
|
4 |
N2/Air |
3~4 |
3000 |
5000 |
100 |
12~16 |
0.5 |
-1~-1.5 |
Single:3.0
|
6 |
N2/Air |
1.2~1.5 |
3000 |
5000 |
100 |
12~16 |
0.5 |
-2~-3 |
Single:3.5-4.0
|
8 |
N2/Air |
0.5~0.6 |
3000 |
5000 |
100 |
16~18 |
0.5 |
-3~-4 |
Single:4.0
|
|
Thicknesses in green indicates it can be processed for long periods of time and in large batches. |
Thickness in yellow can be processed in small batches, but with the increase of material temperature, the cutting air pressure fluctuation, uneven plate composition and other factors fluctuate, and the processing process may be unstable. It is recommended to use a higher power laser. |
Thickness in red can be cut, can be proofing, But is not suitable for batch processing. |
Remark |
1. This cutting data adopts Procutter C9 F200 (+15 to -30) automatic focusing cutting head, and the optical ratio is 100/200 (collimation/focusing mirror focal length); |
2. Cutting auxiliary gas: liquid oxygen (purity 99.99%), liquid nitrogen (purity 99.999%), Air (oil and water filtration); |
3. The air pressure of this cutting data refers to the monitoring air pressure at the cutting head; |
4. Due to the differences in equipment configuration and cutting process (machine tool, water cooling, environment, cutting gas nozzle and gas pressure, etc.) adopted by different customers, this data is for reference only. |
Equipment characteristics
Machine tool
The machine tool is welded as a whole, and processed after annealing to eliminate the internal stress. The process is welding→annealing to eliminate the internal stress→roughing process→vibration aging→finishing process, which better solves the stress caused by welding and processing, thus greatly improving the stability of the machine tool and maintaining the accuracy of the machine tool for a long time.
The company has gantry processing department and machining processing department, which are mainly for the production of all the company's complete sets of machine tool, beam, base and other machine parts. Distinguished from other laser integration manufacturers, all the structural parts of our company are independently processed by us and without any other external producing products. The processing quality is consistent with the product quality, the production period of the equipment is guaranteed, and it is linked with the final quality of the product, so that the quality of each laser product in dapeng laser is consistent.
The machine tool is spliced with square pass structure and the guide plate is made of 30 mm base plate + welding.
There are 2 air ducts inside the machine bed to form a Y-shaped air extraction structure, and the diameter of the air duct is enlarged to 250 mm, which creates a more smooth ventilation duct and ensures excellent air extraction effect.
The air extraction square pass (250*250mm) on both sides is installed with compartmentalized the air extraction device.
There are 2 worktable guide plates on the left and right,with thickness 16 mm.
The machine tool is equipped with double rack, double guide and four sliding-block drive structure. The guide rail uses SHAC brand, and the heavy load type H class (advanced) precision. The protective cover is the fully-enclosed, light fire and oil-resistant type. The rack uses SHGH series of JT brand from Taiwan, and M2 oblique teeth of 6 level precision.
The bottom of the machine bed is a side pumping hopper, which is convenient for discharging materials, and the narrower width is conducive to dust removal; The ground foot is the newly designed ground foot adjustment support, which can enhance the overall stability of the machine after testing; The ventilation area is closed all around for better ventilation effect. The gradient type air extraction sealing plate ensures the effect of the front end of the machine without increasing the segmented air extraction.
The surface of the new guide rack adopts optimized design, and minimizes processing, saves cost, and increases the oil return structure of the guide rail, which can realize automatic lubrication of the guide rail in the later stage, and no longer uses manual yellow oil pump, greatly avoiding the situation of wearing the guide rail because the customer does not butter on time.
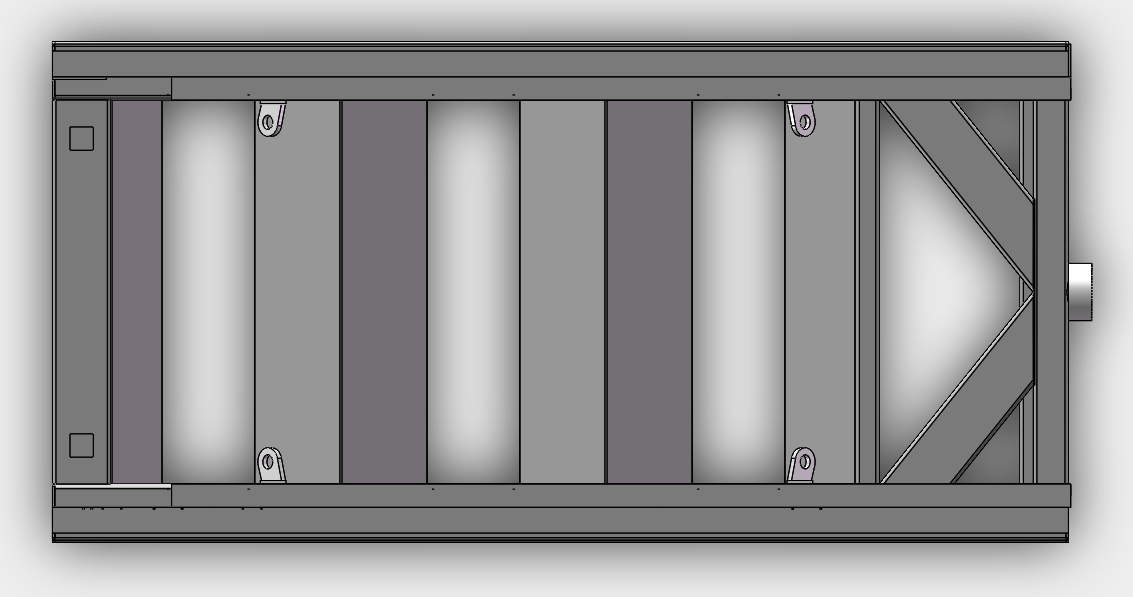
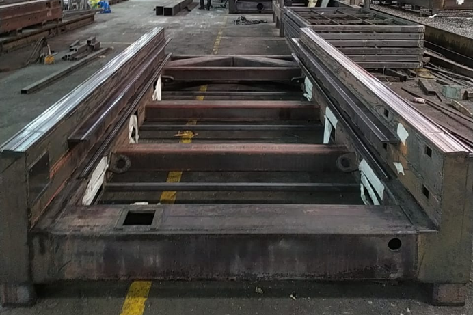